Quality
Ensuring Quality and Safety
Fiscal 2023 Objectives | Fiscal 2023 Achievements | Self-Evaluation | Priority Objectives for Fiscal 2024 |
---|---|---|---|
|
|
★★ |
|
- Self-evaluation::
- ★★★ Achieved more than targeted
- ★★ Achieved as targeted
- ★ Achieved to some extent

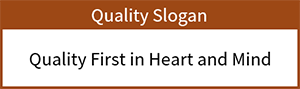
Basic Stance and Vision on Quality
To gain customer trust and improve customer satisfaction, based on its Quality Philosophy and Quality Slogan, the Sharp Group constantly strives to respond to customer needs and demands by providing products and services that are safe, high quality, and reliable.
Quality Assurance System
Under the supervision of the president, the company-wide quality department leads governance and supports related efforts for the entire Sharp Group, with each business unit and affiliate taking responsibility for their respective products. Company-wide functional divisions and business departments collaborate to continuously improve product quality.
Sharp Group’s Quality Assurance System
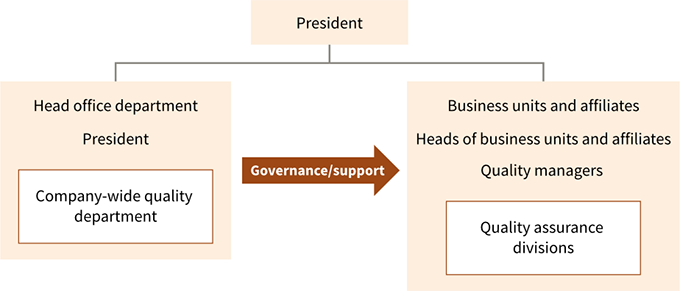
Quality Management System
To enable it to conduct a variety of quality assurance activities in all stages of the manufacturing cycle, including planning, design, procurement, production, assessment, and after-sales, the Sharp Group established the Sharp Corporation Standard based on the ISO 9001 international quality management standard. Stipulating systems and methods necessary for quality assurance, the Sharp Corporation Standard is strictly adhered to by all Sharp sites in Japan and other countries, and by consolidated subsidiaries carrying out design, production, and sales.
Through ongoing revision and implementation of the standard, all employees—in product planning, design, production, sales, and after-sales service—know exactly the level of quality they should be guaranteeing customers in Sharp’s continuous efforts to improve quality.
As of April 30, 2024, 40 of 42 sites are certified for quality management systems*1. The certification rate is 95.2%.
Quality Assurance Activities in the Product-Making Cycle
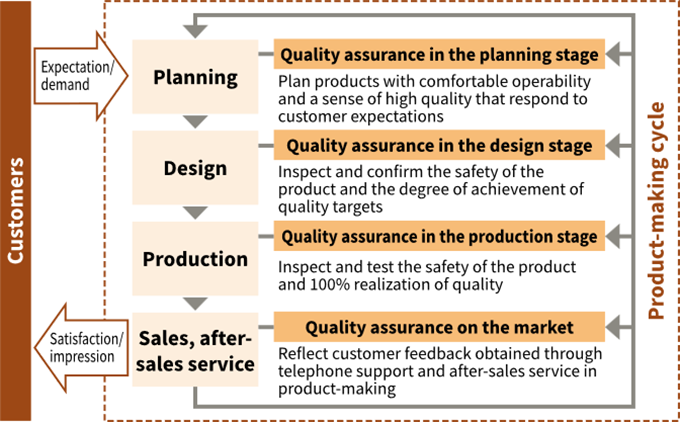
Quality Policy
In line with the Quality Policy stipulated in Sharp Corporation’s company rules (Quality Assurance Basic Rules), the Sharp Group sets quality targets and makes plans to achieve these, implementing these plans by using the PDCA cycle towards achieving the targets.
Quality Policy
Provide high quality and attractive products that customers can continuously use them with safety and satisfactory.
- Observe laws and regulations and place top priority on safety and reliability.
- Pursue convenience and comfort from usability.
- Squarely face with voice of the customer and reflect it in products
Efforts to Improve Quality
As a way to advance quality technologies, the Sharp Group has established the Company-Wide Quality Committee, which is chaired by the president and includes the general managers of each business unit and the presidents of affiliated companies. The Committee carries out improvement initiatives to boost quality company-wide by formulating annual quality-related targets, checking progress on quality KPIs (key performance indicators) that have been set, and having committee members work together to confirm activities towards achieving these targets.
In addition, a Quality Strategy Promotion Committee comprising quality managers from the various business units is convened under the auspices of the Company-Wide Quality Committee to serve as a forum for discussing specific quality measures. Issues that span the entire Sharp Group or multiple business units are taken up by topic-specific expert subcommittees, made up of experts from the various business units, which work to find prompt solutions.
Company-Wide Quality Committee System
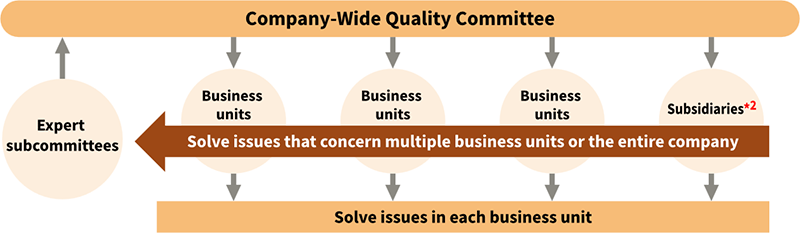
- ISO 9001, IATF 16949 (automotive quality management system), ISO 13485 (medical devices quality management system), etc.
- Subsidiaries of Sharp business unit status.
Fostering Quality Experts
Fostering Quality Experts
Based on its Quality Philosophy, Sharp works to foster quality thinking and boost quality-related techniques by carrying out systematic quality-related education with the aim of making products that customers can use with safety and peace of mind.
In particular, the company is stepping up basic training through programs that allow young employees (in their first four years with the company) to gradually acquire quality-related techniques.
QC Practical Training System
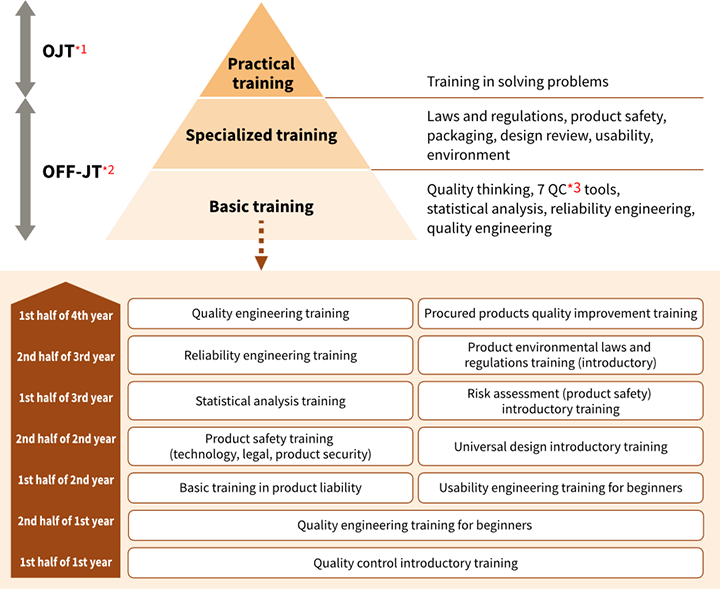
- OJT: On the Job Training.
- OFF-JT: Off the Job Training.
- QC: Quality control.
Sharp implements training in a variety of forms and formats adapted for different educational objectives. First, there are e-learning programs and videoconference classes, which are used to help maximize learning efficiency. There are also group training courses to improve practical skills, which are carried out at the different business units and affiliated companies. In fiscal 2023, there were 34 courses in quality training, with a total of 9,186 participants.
Fiscal 2023 Training Courses and Number of Participants
Training form | No. of course | No. of participants |
---|---|---|
E-learning | 23 | 8,505 |
Group training | 11 | 681 |
Total | 34 | 9,186 |
Ensuring Product Safety
Sharp Voluntary Product Safety Action Policy
Keenly aware that product safety assurance is the most important aspect of a company’s business and one of its social responsibilities, Sharp strives to provide customers with safety and peace of mind. It does this by prioritizing the safety of the products it manufactures and sells and by making safety-related information public. To this end, the company has formulated voluntary action guidelines on product safety in efforts to earn an even higher level of trust from society.
Efforts to Ensure Product Safety
Sharp strives to ensure its products are safe and to constantly raise levels of safety. Besides abiding by laws and regulations of countries and obtaining safety certifications through activities such as factory audits by third parties, the company utilizes its own risk-assessment-based safety standards. To ensure safety even in cases where unforeseen defects arise, these in-house safety standards stipulate items like flame-retardant construction and testing for abnormal conditions. These standards are revised as needed and are taught to all relevant employees in design, quality, and other divisions so that they are understood and followed thoroughly.
Since fiscal 2020, Sharp has been striving to expand the practice of risk assessment related to product safety. Besides providing skills improvement courses via e-learning, we have been strengthening our risk assessment system by appointing a risk assessment manager in each business unit with the goal of developing increasingly safer products.
Sharp will continue to step up efforts to promptly respond to social changes and legal revisions regarding product safety so that customers can use Sharp products with peace of mind.
Initiatives to Strengthen Risk Assessment
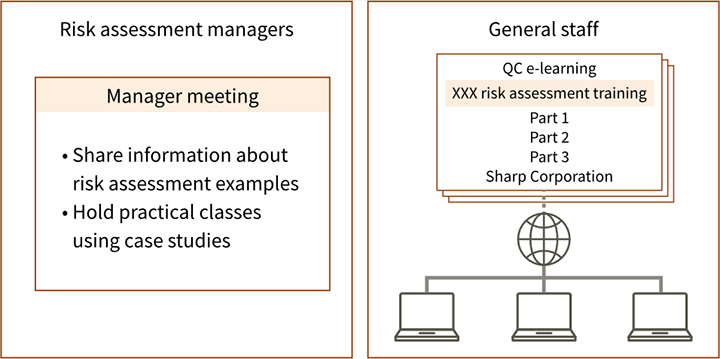
Information Disclosure and Response When Problems Occur
If an accident caused by a Sharp product occurs on the market, the company immediately gathers information on the accident and analyzes it to determine the cause. If it is determined that there is a risk of harm or damage to the customer, information is promptly disclosed via media such as newspapers and the Sharp website, and all appropriate measures are taken to ensure the safety of customers.
For major product-related accidents stipulated in the Consumer Product Safety Act, the Sharp website, in line with the Sharp voluntary product safety action policy, has information on major product-related accidents for which the cause is thought to be the product itself.
Flow for Dealing with Product-Related Accidents

- BRM: business risk management
Product Security Policy and Efforts
Products connected to networks are exposed to growing risks as information technology advances and the value of information they handle increases. They are at a risk of cyber-attack taking advantage of their vulnerabilities, which can result in information leakage or a hijacking of the device being hacked. Security measures once considered adequate are now seen as insufficient, owing to technological advances and other factors. Around the world, there is an urgent and growing need to improve legislation on product security.
Such a situation has been prompting Sharp to act to ensure that customers can use its products without worries. We have established teams and reporting lines dedicated to enhancing product security, along with the rules to be followed at the stages of planning, developing, operating, and maintaining products. Based on a vulnerability information disclosure policy, we gather information on vulnerabilities and work to minimize their risk. We have introduced an e-learning program into employee education in efforts to boost their knowledge and skills in product security as we continuously strive to ensure that customers can feel safe and secure using Sharp products.
We are expecting a future in which standalone systems are interconnected with one another, perhaps creating added vulnerabilities. To prepare for such a future, the Sharp Group has adopted security by design, a concept that intends to build in security from early stages before design. Efforts like these are part of Sharp’s ongoing aim of improving product security and providing products that customers can use with peace of mind.