Promoting Occupational Safety and Health
Sharp Group Basic Policies on Safety and Health
Basic Philosophy
The Sharp Group regards protecting the safety, security, and health of employees all over the world as indispensable to its business activities, and is dedicating appropriate management resources in a spirit of Sincerity and Creativity, in order to achieve a safe and pleasant working environment.
Basic Policy
1. Legislative Compliance
In addition to strict compliance with legislation related to safety and health in each country and region, all Group companies must comply with in-house standards established in line with the standard Group policy.
2. Establishment of Management Organization
The Sharp Group has established a management organization to deal with safety and health, with clearly delineated roles, authority, and responsibilities, and is promoting activities at the structural level.
3. Establishment and Operation of Management System
The Sharp Group has established an occupational safety and health management system, and is engaged in continuous evaluation and improvement of its activities, with a view to eliminating potential hazards and risks to safety and health in the workplace.
4. Implementation of Education and Training
The Sharp Group is endeavoring to raise awareness of safety and health and to promote voluntary activities by implementing for all employees the education and training required to improve safety and health.
5.Setting Targets and Full Employee Participation in Practical Activities
The Sharp Group sets targets for preventing accidents and improving employees' health, and is striving to meet these targets by means of practical activities in which all employees participate.
Organization Promoting Safety, Hygiene, and Health
Sharp works to ensure the safety and to maintain and improve the health of all of its employees, as well as further the creation of a pleasant working environment. Towards that end, it has developed a clear administrative responsibility system for preventing industrial accidents and improving occupational safety and health levels. Also, in order to show Sharp’s commitment to maintaining and improving health, it calls the names of its organizations and activities “safety, hygiene, and health” instead of “safety and health” and has established the following organizational system for promoting safety, hygiene, and health.
In order to ensure that activities for the maintenance and improvement of safety, hygiene, and health go smoothly, Sharp holds Central Safety, Hygiene, and Health Committee meetings that bring the management and the labor union together to discuss and decide basic policies for the entire company. The Committee establishes annual company-wide policies, objectives, and priority action items related to safety, hygiene, and health and rolls them out to business sites and affiliated companies.
At each business site or affiliated company, the Safety, Hygiene, and Health Committee consisting of labor and management representatives, as well as chemical, electrical, and gas subcommittees, meets every month to report, discuss, and review safety, hygiene, and health activities. The discussion and decision outcomes are communicated to all employees through the various departments.
In addition, in order to establish comprehensive safety, hygiene, and health management on company premises, every month at each business site a Safety and Hygiene Council meeting is convened, which includes subcontractors permanently stationed on-site. This committee discusses safety, hygiene, and health-related policy, targets, and planning, shares updates about safety, hygiene, and health initiatives, and works to prevent industrial accidents.
Organization Promoting Safety, Hygiene, and Health

Fiscal 2023 Objectives | Fiscal 2023 Achievements | Self-Evaluation | Priority Objectives for Fiscal 2024 |
---|---|---|---|
|
|
★★ |
|
- Self-evaluation:
- ★★★ Achieved more than targeted /
- ★★ Achieved as targeted /
- ★ Achieved to some extent
Occupational Safety and Health Management System
Sharp has established an occupational safety and health management system and is promoting measures to ensure the further penetration and establishment of “proactive safety,” an initiative under which potential workplace accident risks are identified in advance through risk assessments and eliminated or reduced.
Four of Sharp’s major business sites in Japan have received certification for ISO 45001, an international standard for management systems of occupational safety and health. Sharp has also established and is promoting occupational safety and health management systems at other workplaces and affiliated companies to promote systematic, organized, and continuous safety and health management and raise the level thereof.
Initiatives to Reduce Industrial Accidents
The Sharp Group implements continuous safety management at its work sites in compliance with safety-related laws and company rules as well as provides ongoing safety education to employees.
When industrial accidents do occur, Sharp analyzes their causes, implements effective countermeasures, and then rolls these out at each workplace to prevent reoccurrence. In addition, Sharp is making stronger efforts to foster a safety culture within the company by repeatedly stressing the importance of putting safety first, such as by providing easy intranet access to accident case studies, company policies, regulations and rules, and safety tools that summarize the actions that each employee should take to prevent unsafe behavior, which is the most common cause of industrial accidents.
As a result of these efforts, in the Sharp Group in Japan in fiscal 2023, there were no industrial accidents resulting in death (a record that has continued since fiscal 2013), and our industrial accident rate (frequency rate of lost-worktime industrial accidents*) was 0.36, which continued to be lower than the national average for all industries (2.14), the manufacturing industry (1.29), and the electrical machinery, equipment, and supplies manufacturing industry (0.54).
- Indicator that represents the incidence of industrial accidents per million work hours (one day or more of suspended operations).
Activities to Reduce Industrial Accidents
Item | Description |
---|---|
Safety compliance check |
|
Safety measures at production sites |
|
Safety e-learning |
|
Sharp Group workplace safety website |
|
Displaying company-wide safety awareness posters |
|
Raising awareness of dangers |
|
Annual Industrial Accident Rates (Frequency Rate of Lost-Worktime Industrial Accidents)
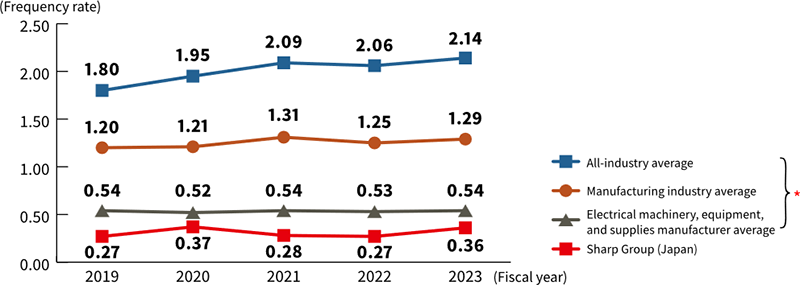
- National averages for all industries, the manufacturing industry, and manufacturers of electrical machinery, equipment, and supplies are based on a 2023 survey by the Japanese Ministry of Health, Labor, and Welfare.
Company-Wide Health Initiatives
The Sharp Group’s business philosophy states that “It is the intention of our corporation to grow hand-in-hand with our employees.” To this end, the Sharp Group has been working together with the Sharp Workers Union and the Sharp Health Insurance Association to support the health of employees through Healthy Sharp 23, a company-wide initiative conducted since fiscal 2014. Starting in fiscal 2023, this initiative was relaunched as Healthy Sharp and has a focus on cancer, cerebrovascular disease and heart disease prevention, as well as prevention of lifestyle diseases like arteriosclerosis, diabetes, hypertension, and dyslipidemia, which are risk factors for cerebrovascular disease and heart disease. Since the onset of these diseases is closely related to daily lifestyle habits, Healthy Sharp focuses on five lifestyle-related factors ((1) diet, (2) exercise habits, (3) sleep, (4) smoking and (5) drinking), along with (6) prevention of mental health disorders, as its target management factors. The aim is to check whether the answers given to questions asked during health checkups satisfy the healthy lifestyle habit indicators and then to increase the percentage of people who satisfy each.

Healthy Sharp—Five Lifestyle Habit-Related Target Management Factors
Target management factors | Regular health checkup questionnaire (medical examination items) | Desired answer |
---|---|---|
(1) Diet | Eats faster than other people | No |
Eats dinner within two hours before bedtime three or more times a week | No | |
Eats snacks or other food in addition to three meals every day or sometimes | No | |
Skips breakfast three or more times per week | No | |
(2) Exercise habits | At least two days per week, performs exercise that lasts for at least 30 minutes per session and produces a light sweat | Yes |
Performs physical activity equivalent to walking for at least one hour per day | Yes | |
Walks faster than others of the same age and sex | Yes | |
(3) Sleep | Gets sufficient rest from sleep | Yes |
(4) Smoking | Is not a habitual smoker Used to smoke but hasn’t in the last month |
No |
Yes | ||
(5) Drinking | Drinks alcohol every day and drinks two or more standard drinks (180 ml x 2) per day, or three or more standard drinks (180 ml x 3) five to six days per week, three to four days per week, one to three days per week, or one to three days per month | No |
Making Employees Healthier
Sharp reviews the lifestyle habits of all its employees based on the regular health checkup questionnaire (medical examination items) and uses the Healthy Sharp initiative as a way of fostering improvement of those habits. The main approaches used include health education and information provision to employees, consultations and health guidance from industrial physicians and public health nurses based on the results of regular health checkups, and various health promotion measures that support improvement of lifestyle habits. Sharp also has ongoing, focused activities to follow up on employees’ health. For example, employees who are at risk of brain or heart diseases are encouraged to undergo health checkups.
Target factors for management | |||||
---|---|---|---|---|---|
(1) Diet | (2) Exercise habits | (3) Sleep | (4) Smoking | (5) Drinking | |
Education/information dissemination |
|
||||
|
|||||
Consultation |
|
||||
|
|
|
|
|
|
Other measures |
|
|
|
|
Enhancing Mental Health Care
Sharp is promoting better mental health by making the prevention of mental health disorders one of its company-wide Healthy Sharp health initiative target management factors.
Sharp is working proactively to increase the rate of participation in the legally mandated stress check system, thereby contributing to the prevention of mental health problems by helping employees become aware of their own stress levels, and implementing early detection and treatment for highly stressed individuals through one-on-one guidance. Sharp is also implementing work environment improvement initiatives in departments with a high proportion of highly stressed individuals and in departments with a high overall health risk based on the results of analysis for each organization.
Sharp also offers comprehensive mental health services to employees, including consultations for new employees and employees working long hours, counseling with mental health doctors and workplace counselors and counseling at outside specialized institutions. Mental health information is also made available to employees on the intranet.
Our return-to-work support program also demonstrates our commitment to supporting reinstatement after absence and prevention of a recurrence of mental health issues. Employees returning to work will have a preliminary talk with the workplace physician and their department, and they can choose to return to work on a trial basis and work shorter or flexible hours.
Initiatives to Improve Employees’ Mental Health

Seminar on Mental Health Measures
Since the pandemic, mental health issues have become more serious, especially among young workers. SVN, Sharp’s sales base in Vietnam, recognizes employee mental health care as an issue that human resources personnel must focus on and is working to create a support system. SVN took part in an external seminar and, based on evidence-based opinions from experts, examined the close relationship between mental health and employee engagement, as well as approaches to mental health care within a business context. Seminar participants learned about the impact that mental health issues and disorders, such as burnout, have on individual employees and business, how to identify mental health issues within teams, how to proactively address them, and how to foster a culture that supports employees and encourages mental care.
Preventing Health Problems Caused by Overwork
Sharp strives to prevent health problems caused by overwork, such as by curbing long working hours, so that all employees can work in full physical and mental health.
Sharp Code of Conduct (excerpt)
We will actively make efforts to create a safety-first workplace environment and to manage proper working time and the like by placing maximum priority on human life, and by complying with global standards, the laws and regulations and internal company rules relating to work conditions and occupational health and safety.
Specifically, in order to limit the amount of overtime work, Sharp has set upper limits on working long hours and has designated days on which no overtime is allowed. Other measures which Sharp utilizes are securing break times between the end of working hours and the start of the next and mandating physician consultation and guidance for employees working long hours.
Measures Related to Work Hours
Item | Description |
---|---|
Upper limits on overtime work |
|
No overtime days |
|
Rules to secure rest time |
|
Encouragement to take scheduled annual paid leave |
|
Criteria for mandatory physician consultation and guidance |
|