


|

 |
The most advanced facility for the integrated production of LCD TVs from the manufacturing of LCD panels to assembly of final products was completed in Kameyama, Mie Perfecture, Japan, and started operation. The plant also provides rationalization in the process of production, inspection and delivery, as well as technology development, resulting in high production efficiency and high value-added performance.
Sharp will be building a second plant at the Kameyama site, with start of production targeted for October 2006.
Plant No. 2 will adopt large-size 8th generation glass substrates of 2,160 x 2,400 mm, which are optimum for the production of 40-inch-class and 50-inch-class models. Eight 40-inch-class panels or six 50-inch-class panels can be obtained from this single 8th generation substrate. Compared with the substrates of Plant No. 1 (1,500 x 1,800 mm for eight 32-inch-class panels) the size will be roughly double.
With the expansion of the supply of large LCD panels from the Kameyama factories, Sharp is greatly advancing LCD TV production to meet increasing market needs.
|
|
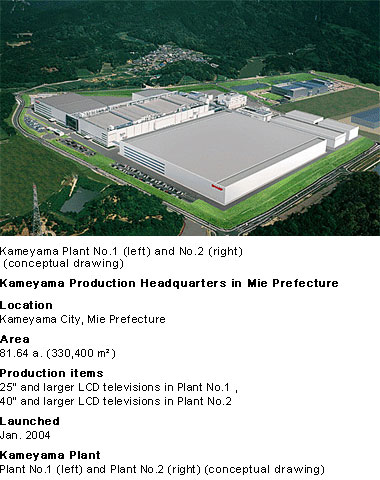
|
 |

|
|
The Kameyama Plant operates with significantly less of a burden on the environment.
As the compilation of SHARP's environmental protection technologies, the plant is the first “Super Green Factory.”
In preparing for construction, we carefully considered environmental protection, beginning at the initial design stage. Working in consultation with local governments and nearby residents, we scrutinized aspects of the project that would be subject to environmental protection measures. We examined the standards that would apply, and confirmed them through evaluation by independent experts. Prior to construction, we transported trees from the site to another location, then replanted them around the factory once construction was complete, thereby mitigating the impact on the local eco system.
|
 |
 |
|
The Kameyama Plant generates one-third of its annual electricity, 12,000kW, using liquefied natural gas (LNG), and utilizes generated waste heat for air-conditioning, hot-water and steam. Emission of CO2 decreased by about 40% from the previous level. LNG volume equivalent to that of 12 tanker trucks is supplied by a 17-km pipeline from the city of Suzuka to Kameyama, which eliminates auto exhaust caused by truck transportation.
|
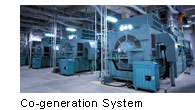 |
 |
 |
|
Six hundred solar-cell modules modeled after the AQUOS design are installed on the walls of the administrative building between the factory for panels and the factory for TV sets. Together with the 200 modules on the walls of the co-generation building, about 48,000 kWh is generated a year.
|
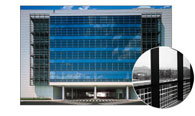 |
 |
 |
|
The plant collects all the wastewater from the production of liquid crystal panels and other processes (max. 9000 tons a day) and recycles it 100% with water purification techniques using microorganism treatment. Foul-smelling wastewater containing chemicals is deodorized by using peat moss.
|
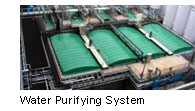 |
 |

|
|
As a global company, to fulfill our social responsibilities for tasks for both the company’s growth and environmental protection, SHARP Corporation has set the long-term vision of increasing production of energy-creating products as well as achieving energy-saving systems in our factories. We strive to implement this vision by decreasing emissions of greenhouse gases from our factories so that the volume of emitted greenhouse gases by SHARP's worldwide business activities equals the volume of decreased gas from energy-creating products by fiscal 2010.
|
|
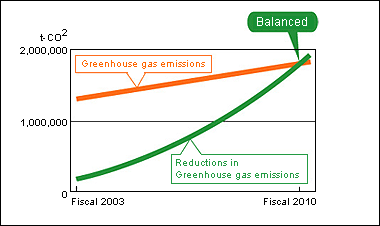
|
|