Business Case Study
NABESEIGLORY CO., LTD.
A two-story warehouse solution built on transport robots (AGVs) and projection helps improve work efficiency.
PDF:924KB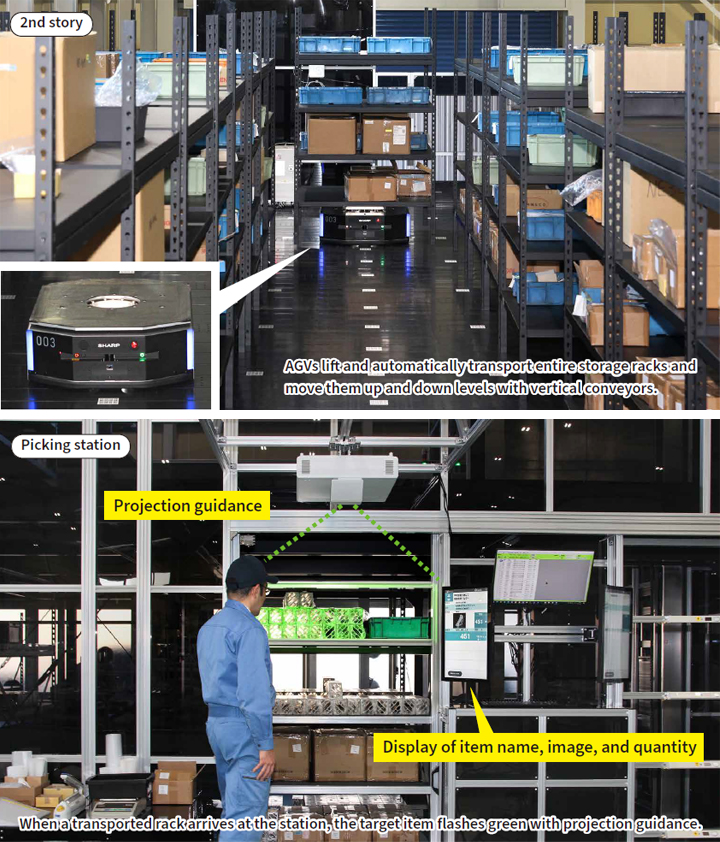
Manufacturing
Improved productivity, Improved efficiency, Enhanced image
Transport robot (AGV) grid model × 3 units
Vertical conveyor × 1 unit, 1 storage set Projector × 1 unit, display × 3 units Centralized control system (AOS), sending/receiving application
Installed in October 2023. AGVs transport storage racks to stations manned by picking operators using a GTP (Goods-to-Person) picking system. Storage racks on the second level are also transported by AGVs using vertical conveyors. When a rack arrives at a station, the system displays images and quantities of target items with the picking list and provides projection guidance for the rack.
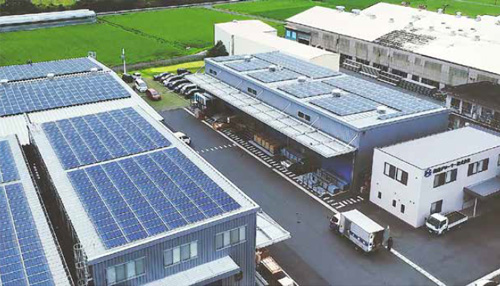
Nagoya, Aichi Prefecture (head office)
A member of the Nabesei (founded in 1877) Group that manufactures aluminum structural materials. NABESEIGLORY handles all aspects of design, manufacturing, and installation of safety covers and fences for use in factories and other facilities.
The Kanie Factory assembles and ships safety covers and other products made primarily with aluminum frames. In the plant’s parts warehouse, workers pick brackets and other parts needed for assembly following lists provided by the design department. However, the large number of similar products meant that workers needed well-developed skills to work without error.
- AGVs transport entire storage racks of parts, eliminating the need for workers to walk around the storage warehouse.
- Projection guidance ensures that no worker will pick the wrong part.
- Inventory management is linked to the company’s shared server. Such management reduces stocktaking and prevents order omissions.
Constant care is needed to avoid picking mistakes.
Our Kanie Factory mainly manufactures aluminum frame-based safety covers and safety fences for use on production lines. Assembling them requires about 250 part types, even when only considering the most commonly used parts. Many similar brackets, nuts, connection plates, and other parts are used to connect frames together. Therefore, workers needed to be very skilled in correctly picking parts from the warehouse according to the design department’s lists. As a result, they were extremely meticulous in component handling, being mindful about preventing mistakes, which led to a significant workload.
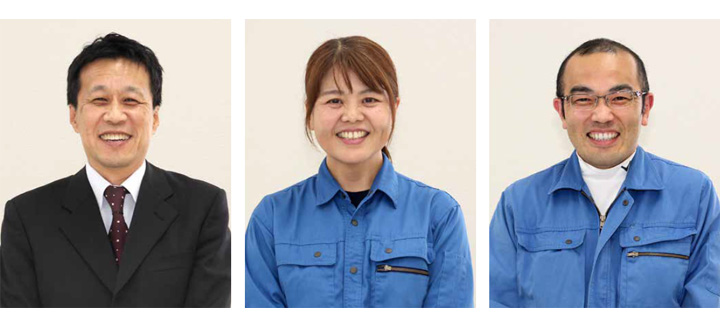
NABESEIGLORY CO., LTD.
(Left)Masaki Nakagawa
Executive Officer and General Manager
(Center)Megumi Kawamoto
Leader
Kanie Factory
Procurement Division
(Right)Joji Ito
Leader
Kanie Factory
Procurement Division
We appreciated the fact that Sharp’s storage system can thoroughly prevent errors caused by human assumptions. When the plan department creates a parts list and enters it into the company’s shared server, the storage system’s AOS server automatically reads it. Then the AGVs automatically transport entire storage racks to the picking station according to the list. The large displays show item names, images, quantities, and other information, and the projection system guides workers around the item racks with a flashing green light to prevent mistakes.
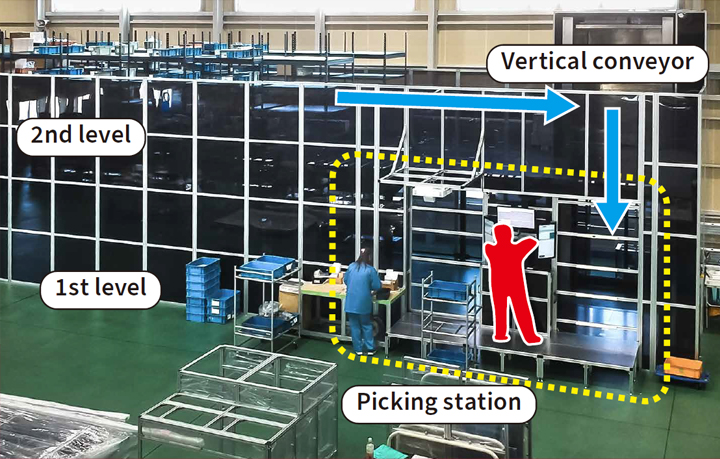
The factory’s parts warehouse was redesigned into a multi-level robotic storage system.
The AGVs transport entire storage racks, thereby eliminating the need for workers to walk around the storage warehouse. Some parts are heavy, weighing 15 kg per case, so transporting them by AVGs means they no longer need to be transferred to a cart, which also reduces the workload. The picking station’s projection system changes the projected light from green to red if a worker accidentally reaches for the wrong rack, ensuring that even inexperienced staff will not make a mistake. Since anyone can now handle picking, hiring and utilizing new workers has become easier, making management easier.
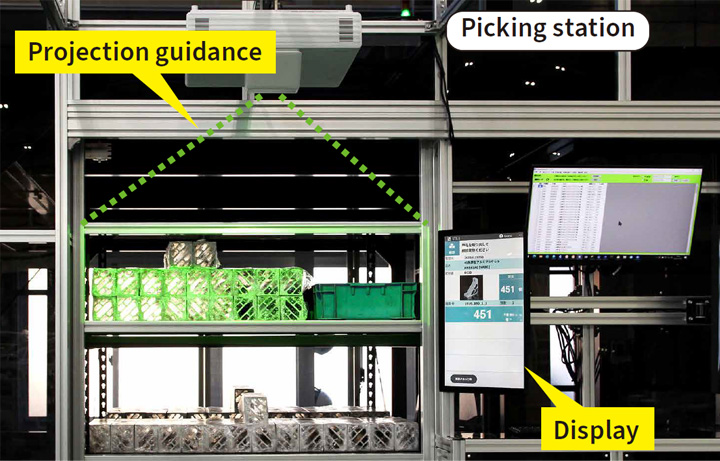
The projection and displayed information prevent picking errors.
Continuing steps toward robotization and automation.
Linking our in-house shared server and the AOS server has made digitalized parts inventory possible and brought better efficiency. Replenishment messages are displayed when inventory levels fall below a suitable level, eliminating order omissions. Since we also have a warehouse for our trading company operations, we will continue studying steps toward further robotization and automation while monitoring the effectiveness of the Kanie Factory’s storage system.
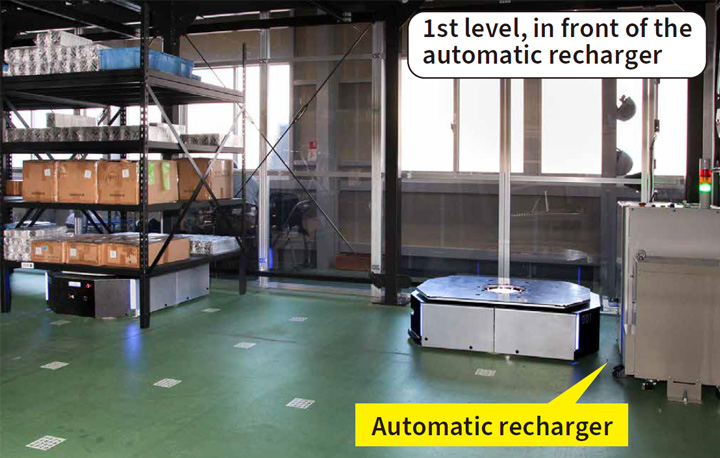
The AGVs automatically transport storage racks and also automatically recharge their batteries.
Issued November 2023