Promoting Occupational Safety and Health
Promoting Occupational Safety and Health
Sharp Group Basic Policies on Safety and Health
Basic Philosophy
The Sharp Group regards protecting the safety, security, and health of employees all over the world as indispensable to its business activities, and is dedicating appropriate management resources in a spirit of Sincerity and Creativity, in order to achieve a safe and pleasant working environment.
Basic Policy
- Legislative Compliance
In addition to strict compliance with legislation related to safety and health in each country and region, all Group companies must comply with in-house standards established in line with the standard Group policy, - Establishment of Management Organization
The Sharp Group has established a management organization to deal with safety and health, with clearly delineated roles, authority, and responsibilities, and is promoting activities at the structural level. - Establishment and Operation of Management System
The Sharp Group has established an occupational safety and health management system, and is engaged in continuous evaluation and improvement of its activities, with a view to eliminating potential hazards and risks to safety and health in the workplace. - Implementation of Education and Training
The Sharp Group is endeavoring to raise awareness of safety and health and to promote voluntary activities by implementing for all employees the education and training required to improve safety and health. - Setting Targets and Full Employee Participation in Practical Activities
The Sharp Group sets targets for preventing accidents and improving employees' health, and is striving to meet these targets by means of practical activities in which all employees participate.
Organization Promoting Safety, Hygiene, and Health
Sharp works to ensure the safety and to maintain and improve the health of all of its employees, as well as further the creation of a pleasant working environment. Towards that end, it has developed a clear administrative responsibility system for preventing industrial accidents and improving occupational safety and health levels. Also, in order to show Sharp’s commitment to maintaining and improving health, it calls the names of its organizations and activities “safety, hygiene, and health” instead of “safety and health” and has established the following organizational system for promoting safety, hygiene, and health.
In order to ensure that activities for the maintenance and improvement of safety, hygiene, and health go smoothly, Sharp holds Central Safety, Hygiene, and Health Committee meetings that bring the management and the labor union together to discuss and decide basic policies for the entire company. The Committee establishes annual company-wide policies, objectives, and priority action items related to safety, hygiene, and health and rolls them out to business sites and affiliated companies.
At each business site or affiliated company, the Safety, Hygiene, and Health Committee consisting of labor and management representatives, as well as chemical, electrical, and gas subcommittees, meets every month to report, discuss, and review safety, hygiene, and health activities. The discussion and decision outcomes are communicated to all employees through the various departments.
In addition, in order to establish comprehensive safety, hygiene, and health management on company premises, every month at each business site a Safety and Hygiene Council meeting is convened, which includes subcontractors permanently stationed on-site. This committee discusses safety, hygiene, and health-related policy, targets, and planning, shares updates about safety, hygiene, and health initiatives, and works to prevent industrial accidents.
Organization Promoting Safety, Hygiene, and Health
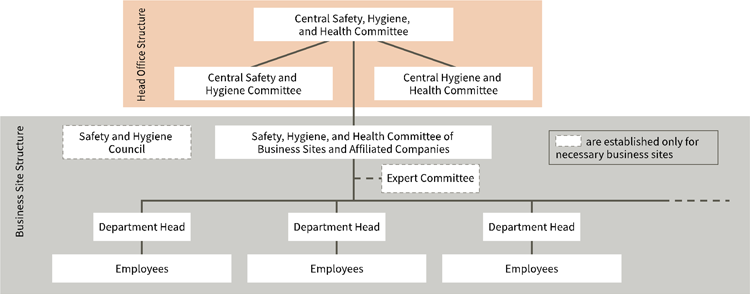
Fiscal 2022 Objectives | Fiscal 2022 Achievements | Self-Evaluation | Priority Objectives for Fiscal 2023 |
---|---|---|---|
|
|
★★ |
|
- Self-evaluation: ★★★ Achieved more than targeted / ★★ Achieved as targeted / ★ Achieved to some extent
Occupational Safety and Health Management System
Sharp has established an occupational safety and health management system and is promoting measures to ensure the further penetration and establishment of “proactive safety,” an initiative under which potential workplace accident risks are identified in advance and eliminated or reduced.
Four of Sharp’s major business sites in Japan have received certification for ISO 45001, an international standard for management systems of occupational safety and health. Sharp has also established and is promoting occupational safety and health management systems at other workplaces and affiliated companies to promote systematic, organized, and continuous safety and health management and raise the level thereof.
Initiatives to Reduce Industrial Accidents
To prevent industrial accidents, the Sharp Group implements effective prevention measures across the organization based on analysis of the causes of accidents.
We also targeted all employees at Sharp Group companies in Japan in fiscal 2022 by, for example, offering safety e-learning and displaying safety awareness posters at bases, efforts which drive home the importance of following safety and procedural rules and help reaffirm awareness of the safety first concept.
In addition, to prevent things that lead to serious industrial accidents, such as falls and crashes, and to prevent accidents caused by reaction to motion and improper motion, we are raising employees’ awareness of dangers by making potential hazards more visible and conducting training in near-miss accidents and danger prediction. At production sites, thorough measures include having employees follow procedural rules and ensuring that equipment is always safe to use.
As a result of these efforts, in the Sharp Group in Japan in fiscal 2022, there were no industrial accidents resulting in death (a record that has continued since fiscal 2013), and our industrial accident rate (frequency rate of lost-worktime industrial accidents*1) was 0.27, which continued to be lower than the national average for all industries (2.06), the manufacturing industry (1.25), and the electrical machinery, equipment, and supplies manufacturing industry (0.53).
Raising Safety Awareness Among All Employees
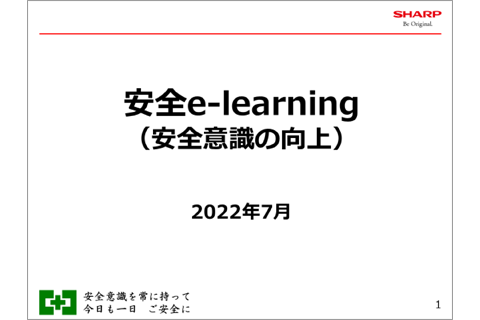
Safety e-learning textbook
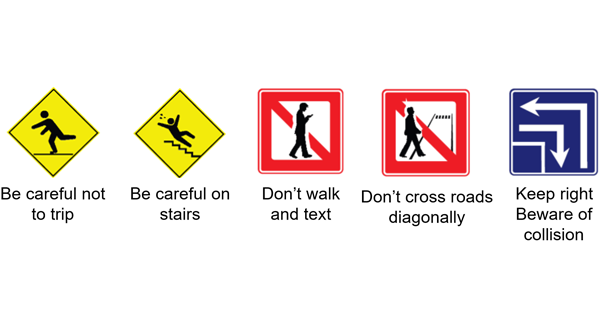
Safety awareness posters displayed at bases
Annual Industrial Accident Rates (Frequency Rate of Lost-Worktime Industrial Accidents)

- *1 Indicator that represents the incidence of industrial accidents per million work hours (one day or more of suspended operations).
- *2 National averages for all industries, the manufacturing industry, and manufacturers of electrical machinery, equipment, and supplies are based on a 2022 survey by the Japanese Ministry of Health, Labor, and Welfare.
Company-wide Health Initiatives
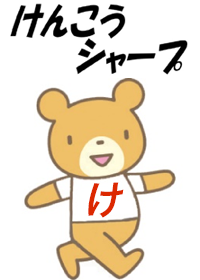
Mr. Get, the mascot for Healthy Sharp
The Sharp Group’s business philosophy states that “It is the intention of our corporation to grow hand-in-hand with our employees.” To this end, the Sharp Group has been supporting the health of employees through Healthy Sharp 23, an initiative conducted since fiscal 2014. With this initiative, the Sharp Group is working together with the Sharp Workers Union and the Sharp Health Insurance Association to achieve the following five targets:
1. Reduce the obesity rate of employees
2. Lower the smoking rate of employees
3. Increase the rate of employees who regularly exercise
4. Reduce the total amount of sick leave associated with mental health issues and disorders
5. Eliminate constant excessive work hours
We will continue in fiscal 2023 and onward with measures to improve employees’ wellbeing through Healthy Sharp.
Making Employees Healthier
Sharp is striving for better employee health in numerous ways. For example, based on the results of periodic health checkups, employees have workplace physician interviews and are provided with health guidance to prevent lifestyle diseases, lose weight, and stop smoking. We have also made all company buildings smoke-free. We also encourage regular exercise through a competitive walking campaign among workplaces, which runs via a smartphone app.
We also have ongoing, focused activities to follow up on employees’ health. For example, we encourage employees who are at risk of brain and heart diseases to undergo health checkups.
Enhancing Mental Health Care
Sharp uses its employee stress check system, which is required under the Japanese law, to let employees realize their level of exposure to stress. The system is expected to lead to the prevention, early detection, and early treatment of mental health issues. Stress check results are also analyzed for each organization, so that we can improve the workplace environment.
Sharp also offers comprehensive mental health services to employees, including counseling with mental health doctors and workplace counselors and counseling at outside specialized institutions. Mental health information is also made available to employees on the intranet.
Our return-to-work support program also demonstrates our commitment to supporting reinstatement after absence and prevention of a recurrence of mental health issues. Employees returning to work will have a preliminary talk with the workplace physician and their department, and they can choose to return to work on a trial basis and work shorter or flexible hours.
Initiatives to Improve Employees’ Mental Health
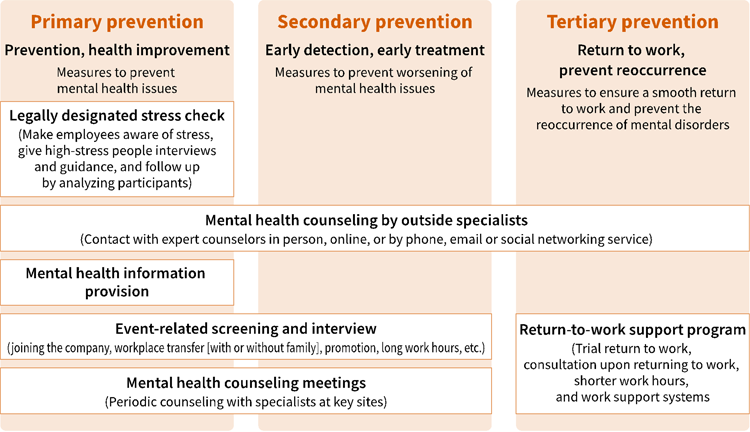
Preventing Health Problems Caused by Overwork
Sharp strives to prevent health problems caused by overwork, such as by curbing long working hours, so that all employees can work in full physical and mental health.
Sharp Code of Conduct (excerpt)
We will actively make efforts to create a safety-first workplace environment and to manage proper working time and the like by placing maximum priority on human life, and by complying with global standards, the laws and regulations and internal company rules relating to work conditions and occupational health and safety.
Specifically, in order to limit the amount of overtime work, Sharp has set upper limits on working long hours and has designated days on which no overtime is allowed. Other measures which Sharp utilizes are securing break times between the end of working hours and the start of the next and mandating physician consultation and guidance for employees working long hours.
The total hours actually worked by Sharp Corporation general staff were 1,745 hours per employee in fiscal 2022, and annual overtime work hours per employee were 76 hours.
Measures Related to Work Hours
Item | Description |
---|---|
Upper limits on overtime work |
|
No overtime days |
|
Rules to secure rest time |
|
Encouragement to take scheduled annual paid leave |
|
Criteria for mandatory physician consultation and Guidance |
|
Promoting Employee Health Management
In February 2023, Malaysian production base SNM participated in a pilot program to self-test for Covid-19.
This program was organized by the Malaysia Ministry of Health in collaboration with the Federation of Malaysian Manufacturers and a global non-profit organization, FIND.
Over 700 employees and their family members participated in the program at SNM. This not only prevented the spread of the disease but also contributed to the health and wellbeing of employees and their families, as well as customers and business partners.
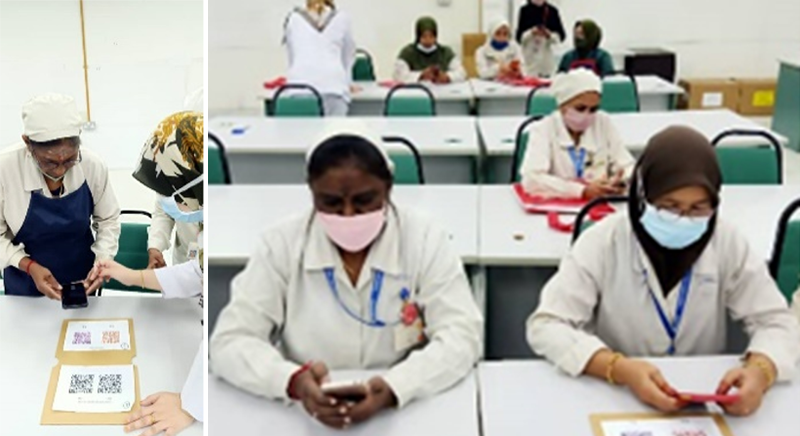
Self-testing for Covid-19